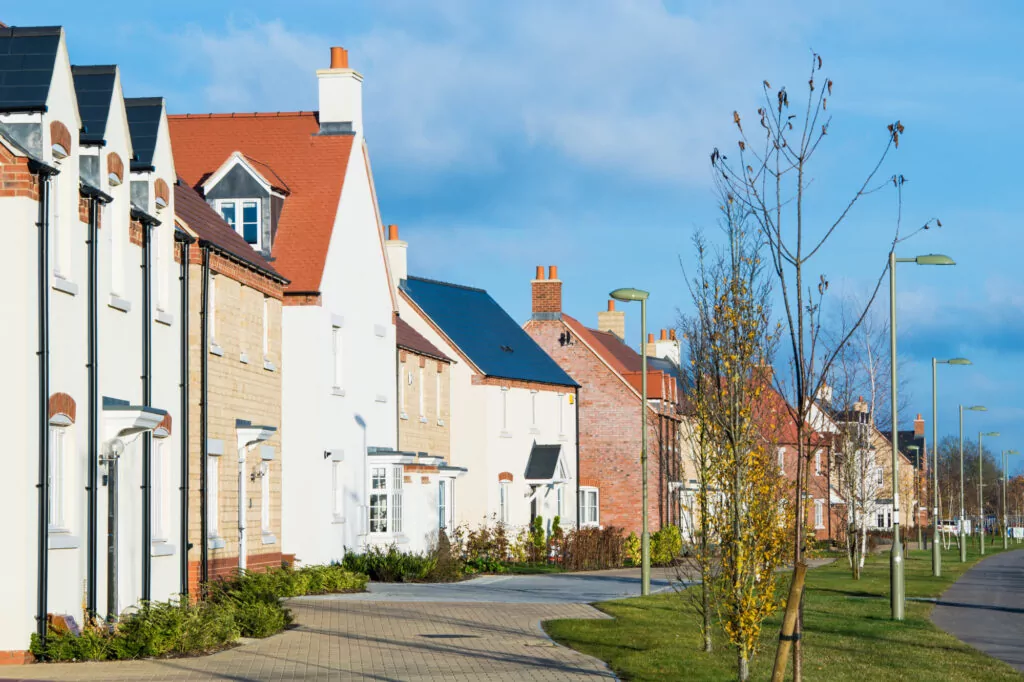
Just what are modern methods of construction (MMC)? The term is relatively self-explanatory: it refers to a number of game-changing innovations within the construction industry intended to improve efficiency and build quality.
MMC is a broad industrial category encompassing computer-controlled off-site manufacturing - of entire building modules for example - along with the use of new materials and contemporary on-site building techniques (e.g. new methods of laying concrete). Digital technology is a central component of MMC, which can function as extension to traditional building techniques or as a complete replacement.
Figures from the Royal Institute of British Architects reveal that, MMC building can reduce the number of employees required on a construction site by up to 70 per cent and cut overall building costs by 20-40 per cent.
Although opinions differ on precisely which construction methods qualify for the title, modular or volumetric construction is perhaps the most prominent.
Modern methods of construction bring several benefits to housebuilding: greater speed and lower labour costs, along with better quality construction and an overall increase in reliability. All this should make MMC a very attractive choice both for developers and governments seeking to encourage the creation of new housing stock. MMC building also means that housebuilders can be less reliant on the need for a steady supply of skilled employees, which which have become increasingly difficult to meet in recent decades.
According to a 2018 report by the National House Building Council (NHBC), close to 30 per cent of UK developers have opened MMC manufacturing facilities for their own developments.
The House of Commons Modern Methods of Construction report
In July 2019, the parliamentary Housing, Communities and Local Government Committee published a report into MMC claiming Britain would fall well short of its ambitious house building targets if modern techniques weren't more widely adopted. The government had previously pledged to oversee the construction of 300,000 homes per year by the mid-2020s but the use of MMC with the house building sector remains relatively low.
MMC, the Committee insisted, would allow an acceleration in the construction of new homes without any sacrifice in build quality - and it urged the government to encourage more construction companies and property investors to fully explore its potential.
Specific measures proposed by the Committee included:
- A government-wide strategy for an increase in the use of MMC, with funding for the latter clearly tracked.
- A greater focus on training and apprenticeship schemes, working in conjunction with the Advanced Manufacturing Research Centre and Homes England.
- Further work to develop centres of excellence in MMC, in conjunction with the Construction Innovation Hub and the Transforming Construction Programme.
- Encouraging industry-wide standardisation of MMC techniques and testing of MMC materials and components.
- Work to strengthen and develop currently patchy supply chains within the industry.
- A single set of warranty standards for MMC techniques and building materials. Currently warranties are manufacturer- or developer-specific.
- Improvements to data collection and sharing to encourage more confidence in MMC amongst lenders, insurers and property buyers. In particular the MPs favoured a national database of homes built using MMC to fully demonstrate their value and durability.
- A government review of current building and financial regulations in order to increase access to land for building and encourage greater overall uptake of MMC across the construction sector, as well as commissioning organisations such as local authorities.
- Efforts to increase access to suitable funding for MMC-based building.
Clive Betts MP, Chair of the Housing, Communities and Local Government Committee, said:
“If the Government is to have any chance of meeting its target of 300,000 new homes a year it cannot simply rely on traditional construction methods. They must make a serious effort to support the use of new and emerging technologies that have the potential to have a transformative impact on the speed, cost and quality of home building. This is not simply about shifting production away from the building site and into factories. It is about seizing opportunities that modern technologies allow, whether it be precision manufacturing, use of new materials or digital working.” He contrasted MMC with the less successful construction innovations of the 1950s and 1960s, “which created homes that failed to survive half a century, while rows of Victorian terraces are still standing.”
Modular/ volumetric construction
Let's take a look at modular construction in more detail.
Also known as ‘volumetric' construction, it is a building technique which replaces the traditional construction - on-site ‘bricks and mortar' - approach with the off-site manufacture of large, three-dimensional ‘modules' in factory conditions. They are made from steel, timber, mixed concrete and similar materials and fitted out with the required fixtures before leaving the factory. They are then transported to the construction site and rapidly stacked together into the finished property using cranes.
‘Hybrid' construction is a variation of the volumetric approach, in which modules are combined with pre-made walls, floors and roofs, called ‘panels'.
Modular construction offers a number of significant advantages, including:
- Off-site construction eliminates the possibility of delays caused by bad weather, removes the need for on-site inspections and significantly simplifies the overall building process, reducing typical property build time from months to weeks.
- Lower costs : both for the construction company, via a reduced need for skilled labour, and for the property purchaser.
- built from the ground-up using modern materials and technology, modular homes benefit from exceptional energy performance and efficiency - and that means lower bills for the occupants. According to the parliamentary report, MMC homes may require 20-30 per cent less energy to heat than conventional housing.
Our services in modular construction
Foot Anstey LLP is a national legal practice which specialises in services to the construction industry. Its expert team works alongside many firms involved in MMC projects, including construction firms, local authorities, housing associations, and property funding suppliers.
The Foot Anstey range of business services includes:Expert advice on property and planning law, construction law, risk management and an awareness of key industry trends that impact clients.Drafting property and construction contracts tailored to each client's specific needs.Dispute resolution.Advice on net zero carbon construction, localised energy generation, mobility and the use of charge points in modular construction.Advice on data and compliance with data protection legislation.
If you are planning a modular build, find out more about our development lawyers or contact us today!