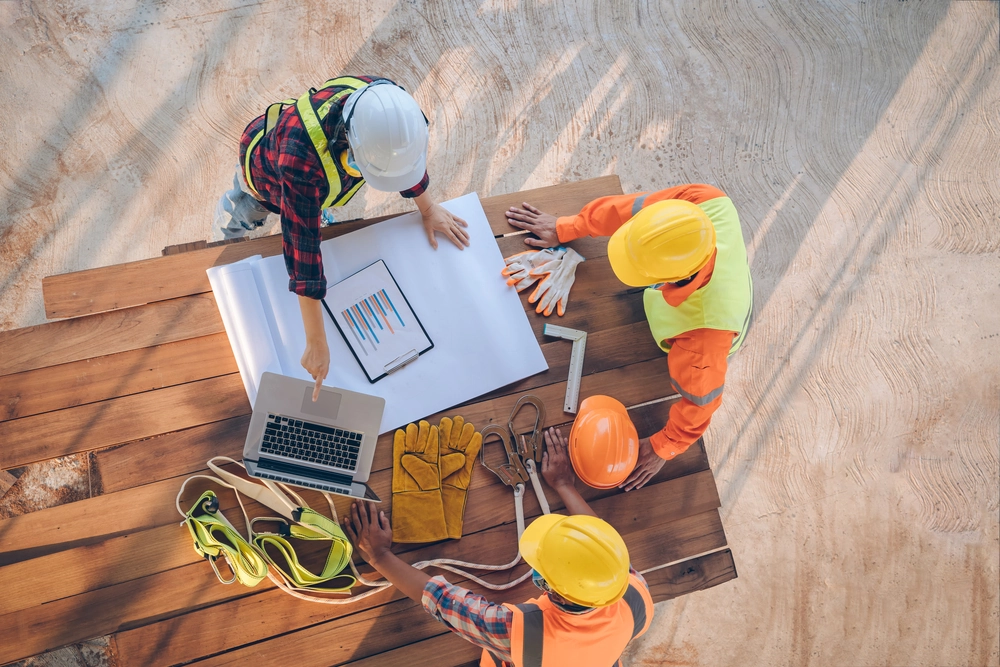
Part 1
Structural defects warranties in modern methods of construction – A Macro view
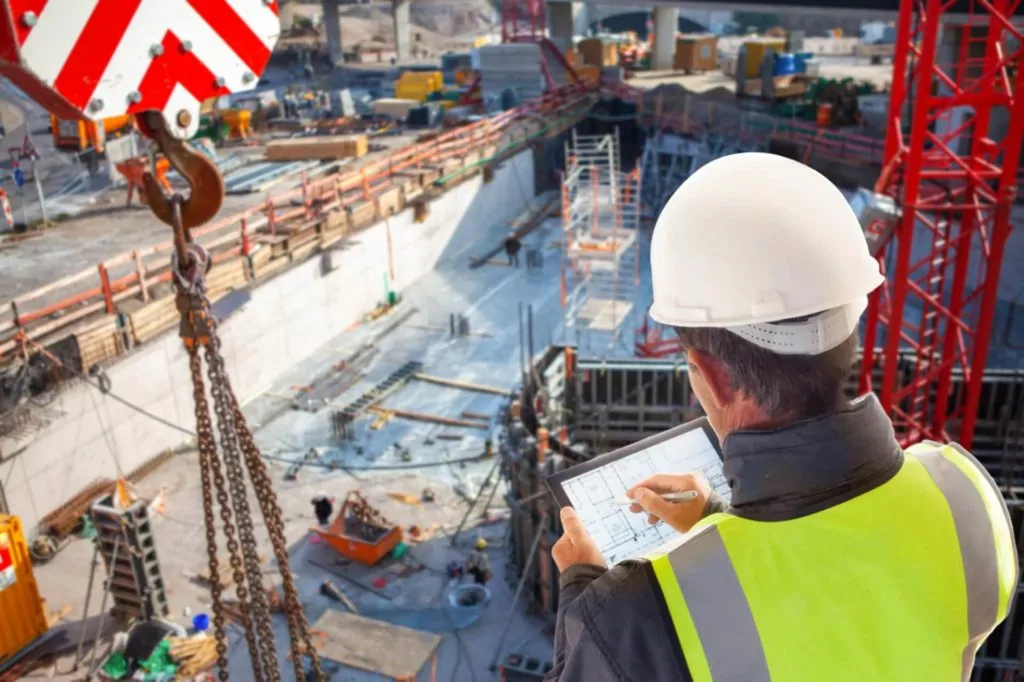
In this two-part article series Foot Anstey and Premier Guarantee explore key issues in respect of structural defects insurance in the context of Modern Methods of Construction ("MMC").
Historically, Commercial Latent Defects insurance provides building owners with protection for defects caused by faults in the design, materials or workmanship in the main structural and waterproofing elements of an insured property.
Policies are typically 10 years in duration (but can be 12 years), non-cancellable and are transferrable to future property owners within the policy period.
The insurance cover goes hand-in-hand with a Technical Audit, which is undertaken as a pre-requisite to the provision of cover. The audit comprises of a check of the design and structural calculations and site visits to assess the quality of construction and the approval of MMC systems.
This today offers an extra incentive in the take up of MMC projects which sits alongside collateral warranties and building control sign off. This is particularly attractive to funders. It also mitigates the risk of contractor insolvency. That is, if there is a latent structural defect the owner is able to trigger the claims process under the policy with the solvent warranty provider, instead of solely relying on a claim against a potentially insolvent contractor.
Structural defects warranties have for years underwritten traditional build, and these have now also evolved to cater to projects incorporating MMC. The fundamental principles remain the same but in these articles we explore some of the macro issues in relation to such warranties, and then drill down to ask Premier Guarantee a few questions arising in the certification processes in part 2 of the series.
The Q&A here is based on questions raised by Foot Anstey to draw out some key themes and issues in the structural defects warranty market. The answers provided by Premier Guarantee set out their industry experience and identify some of the trends and blockers to MMC take-up and acceptance.
1. What key risks/issues do you see with MMC when developers first approach you?
1.1 Key risks we are dealing with in relation to MMC on a daily basis are:
(a) Systemic failure where any defect in design or manufacturing process will be replicated by repetition on every project using the same system
(b) MMC off-site manufactured systems and products used outside of the scope of third-party certification
(c) Issues where the construction industry never managed to provide clear guidance, neither by British or European Standards (i.e. cavity barriers, passive fire stopping in light structures)
(d) Systems manufactured outside of the UK to European standards instead of British Standards in breach of Warranty requirements (i.e. non-treated timber or provision of drained cavity)
(e) Inexperienced individuals and companies switching to off-site industry, and
(f) Lack of quality management systems.
2. What kind of MMC products do you usually see?
At the moment we are dealing with multiple modular and panelised systems. The majority of modular construction is based on hot rolled steel frames with light steel infill panels, panelised systems that are predominantly timber frame and there is increasing interest from pre-cast concrete manufacturers to gain our product/system acceptance.
3. Do you predict steady growth in the use of modular/MMC/other non-traditional construction methods over the next decade?
It is evident that MMC will shape the future of construction around the world. The UK Government framework infusing billions of pounds into our building industry will only speed up the process and push builders and developers to use more sustainable and cost-effective methods. We are seeing increased interest in MMC products and systems used on our schemes, and we are sure that this will only increase in volume.
Modular construction places an emphasis on maximising off-site manufacture of components and minimising on-site assembly and rework time, aiming to reduce the required resources, environmental impact, introduce efficiency, improve productivity and quality of works carried out in a dry controlled environment.
4. In your view, are modular/MMC systems (in general) as robust as their traditional construction counterparts?
Our assessment is based on the same principles as traditional construction methods, we require a minimum of 60 years of design life for all structural elements. Systems that we accept must use third party certified products and therefore we can support our review based on test evidence and independent assessment.
Innovative products and systems pose additional risk due to their short track-record so far in the end use scenario. However, we use our claims experience and available research resources to reduce the risk to a standard level.
Any product, system or design performance could be easily decreased due to poor workmanship or incorrect application, but this is true for both traditional and MMC off-site construction. We believe that systems assessed by our Innovations Team based on appropriate components built in controlled environments with suitable quality management systems in place should equal traditional construction methods.
5. What are the main concerns of mortgagees/funders around security over dwellings built in non-traditional ways?
Durability, maintenance and provision of remedial works to the structural parts are all standard concerns across the board. As modular construction is a new and emerging technology, mortgage lenders have concerns around the lifespan of dwellings (as their requirements are for properties to last a minimum of two mortgage terms) and in some cases there is no historic evidence to demonstrate this.
6. Are warranty systems the only solution for ensuring quality of MMC products? Are there other ways of dealing with accepting systems?
This is dependent on whether the developer/self-builder/client require a structural warranty or the buyer of the property is looking to take out a mortgage on the property as most lenders require there to be a structural warranty on a new build property. Other construction professionals are often involved with ensuring quality such as Building Control bodies, developers using MMC products and manufacturers of the MMC products often provide training on the use of their products and have their own internal Q&A processes to ensure quality.
Every MMC off-site ‘closed panel’ and ‘modular volumetric’ systems must be accepted by the warranty provider prior to the warranty quote being provided. We could accept full system assessment by a third party conformity body, although we would still review system design and specification to make sure it is in line with our warranty requirements which are often above minimum requirements outlined in Codes of Practice and Building Regulations.
To see how our experts could help your organisation, contact us today to learn more about how we can offer solution focused advice in respect of offsite construction. To learn more about the industry experience of Premier Guarantee, please click here.
Please note that Premier Guarantee Acceptance does not constitute a 3rd Party Product Approval from a UKAS Accredited Testing Body or any form of Building Regulation approval. This Premier Guarantee Acceptance is purely to recognize that this system/product can meet our warranty requirements and must not be considered to be anything else.
This article is a collaboration piece to build crucial industry links to positively enable the take-up of MMC and its role in sustainable construction. The authors are Maciej Pulawski (Head of Innovation, Premier Guarantee), Piers Durrant (Marketing Manager, Premier Guarantee), Suriya Edwards (Managing Associate, Construction, Foot Anstey LLP) and Adam Burrage (Senior Associate, Commercial Property, Foot Anstey LLP). For further details on MMC and stress-testing contracts please contact Foot Anstey LLP or for Premier's structural defects warranty please contact Premier Guarantee.